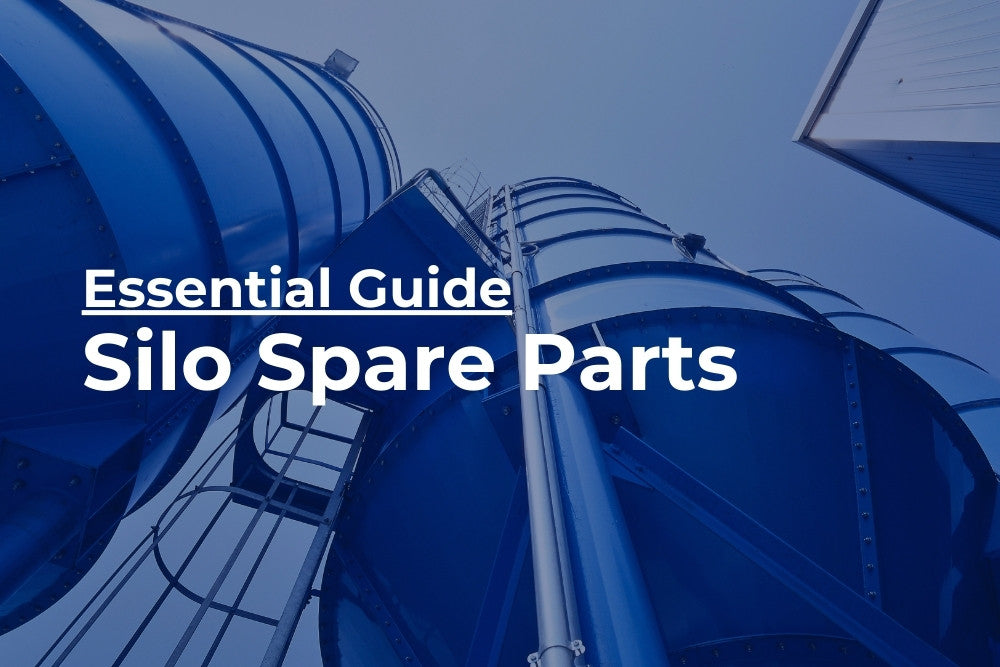
The Essential Guide to Storage Silo Spare Parts | KMH Spares
Storage Silos are vital components in industries such as Construction, Manufacturing, and Agriculture, where bulk materials are stored like cement, aggregates, chemicals and grains. Maintaining the operational integrity of these silos is crucial for safety, efficiency and the loss prevention for vital businesses.
Central to the maintenance is the availability and management of spare parts. We will explore the critical spare parts that ensure the safe and efficient operation of storage silos, focusing on Pressure Relief Valves (PRVs), Inspection Doors, Extraction Valves, Silo Vibrators, Level Indicators and the brain of the brain of it all; electronic control panels.
1.) Pressure Relief Valves (PRVs): Safeguarding Against Overpressure
Pressure Relief Valves (PRVs) are indispensable for maintaining safety in storage silos by preventing over-pressurisation. Overpressure can occur when materials are pneumatically conveyed into the silo, potentially leading to explosions or structural failures. Standards, such as EN 14491:2012, emphasise the importance of explosion venting devices like PRVs for silos handling combustible dusts and powders.
PRVs must be carefully selected based on the silo's design and the material stored. In the EMEA region, it's crucial to adhere to European standards and regulations to ensure compliance and safety. Regular maintenance and testing are necessary to ensure PRVs function correctly, as issues like corrosion or blockages can impede their effectiveness.
2.) Inspection Doors: Ensuring Safe and Easy Access
Inspection doors are another vital component, providing necessary access for maintenance, cleaning, and inspection of the silo’s interior. According to the European Standard EN 1993-4-1, which deals with the design of steel silos, proper access points are crucial for both operational efficiency and safety. These doors allow operators to inspect the interior of the silo for signs of wear, blockages, or material buildup that could affect performance.
When selecting inspection doors, it is essential to consider factors like material durability, seal integrity, and ease of use. For instance, in environments where aggressive materials are stored, stainless steel or aluminium doors may be preferable due to their resistance to corrosion. Regular maintenance of inspection doors, including checks for seal wear and hinge functionality, is critical to ensure they provide a safe and secure entry point.
3.) Extraction Valves: Controlling Material Flow
Extraction valves, including butterfly valves and slide valves, play a key role in controlling the discharge of materials from silos. These valves must provide a reliable seal to prevent leakage and allow for precise control of material flow. The European norm EN 14755:2005 outlines requirements for valves used in bulk handling systems, emphasising the need for durability and resistance to wear, particularly when dealing with abrasive materials like cement or sand.
Butterfly valves are commonly used due to their simple design and ease of operation, while slide valves offer robust sealing capabilities, making them suitable for applications where a tight seal is critical. Regular maintenance, such as checking for seal integrity and wear on moving parts, is essential to prevent operational failures that could lead to material loss or contamination.
4.) Silo Vibrators: Ensuring Consistent Material Flow in Cone Silos
Silo vibrators are used to prevent material blockages and ensure a steady flow of materials within the silo. These devices are particularly important in silos storing materials prone to compaction, such as fine powders or moist aggregates. In Europe, the use of vibrators is guided by the Machinery Directive 2006/42/EC, which sets out safety requirements for machinery, including vibratory equipment.
Choosing the right type of vibrator—whether pneumatic, electric, or hydraulic—depends on factors such as the silo’s size, the material’s properties, and the required vibration frequency. Proper installation and maintenance of vibrators are crucial to ensure they operate effectively. This includes regular checks for wear, securing bolts, and ensuring that the vibrator is properly aligned with the silo structure to avoid uneven wear or damage.
5.) Level Indicators: Monitoring Material Levels in Silos
Accurate level measurement is critical for the efficient operation of silos, helping to prevent overfilling and ensuring timely replenishment of materials. Level indicators, such as radar, ultrasonic, or capacitive sensors, provide real-time data on the amount of material within the silo. The European Standard EN 60079-0 provides guidelines on the use of equipment in explosive atmospheres, which is particularly relevant for silos storing combustible materials.
In the Ireland and the United Kingdom, advanced level indicators that offer remote monitoring capabilities are becoming increasingly popular, allowing operators to monitor silo levels from a central control room. Regular calibration and maintenance of these sensors are essential to ensure their accuracy and reliability, particularly in dusty or harsh environments.
6.) Control Panels: The Brain of Silo Operations
Control panels are the central hub for managing all silo operations, from material inflow and outflow to monitoring and safety systems. Regulations, such as the Low Voltage Directive (LVD) 2014/35/EU, govern the design and use of electrical equipment, including control panels, to ensure safety and reliability.
Modern control panels often include Programmable Logic Controllers (PLCs) and Human-Machine Interfaces (HMIs), which provide intuitive control over silo operations. These systems can be customised to meet the specific needs of the silo, offering features such as automated alerts, data logging, and remote access. Regular updates and maintenance of control panels are necessary to prevent software glitches or hardware failures that could disrupt silo operations.
So WHY is it important to maintain and update Silo Spare Parts?
Proper management and maintenance of storage silo spare parts are crucial for ensuring safety, efficiency, and compliance with regulations. By focusing on the key components—PRVs, inspection doors, extraction valves, silo vibrators, level indicators, and control panels—silo operators in Ireland and the UK can prevent costly downtimes, avoid safety hazards, and extend the lifespan of their silo systems. Adhering to standards and best practices in maintenance will not only enhance operational efficiency but also ensure the long-term safety and reliability of storage silos.